Location: Andros Island, Bahamas
System Applied: JBT 303
Substrate / Area: Concrete / Secondary Containment / 26,000 sq. ft. / 15,500 sq. ft.
Date Completed: Aug 2002, Dec 2002
Quality Control: Primeaux Associates, LLC.
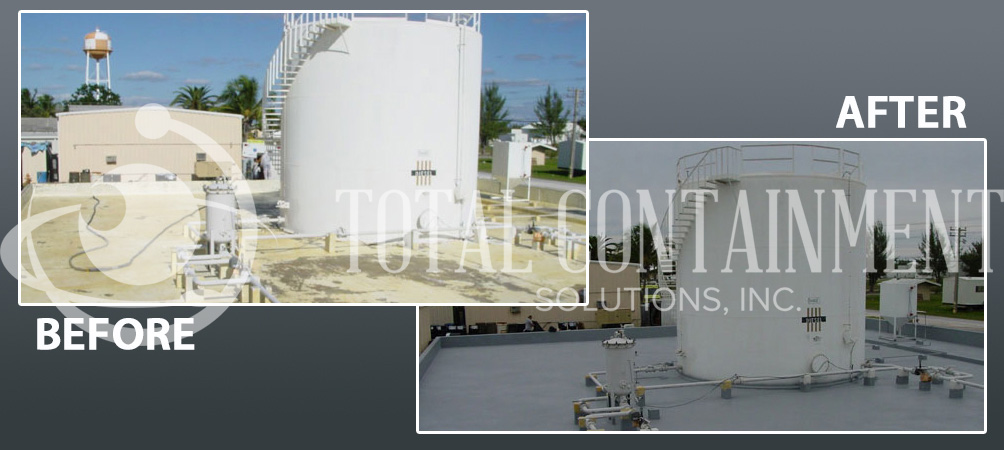
PROJECT DESCRIPTION
The acid containment’s existing paint lined system was failing. The paint lined system was removed and hydro blasted to remove bonding agent. Surface then was neutralized to accept primer. Surface had to be skim coated where acid had deteriorated the containment. P3 primer was applied followed by 60-70 mils of polyurea. A primer coat of PolyVers LC25 Extreme Chemical Exposure Lock Coat was then applied and top coated with PolyVers VT40 Finish Coat. RoboLiner ®was used to replace the old system.
KEYS ENERGY SERVICES
Location: Key West, FL
System Applied: JBT 303
Substrate / Area: Concrete Roof
Date Completed: August 2003
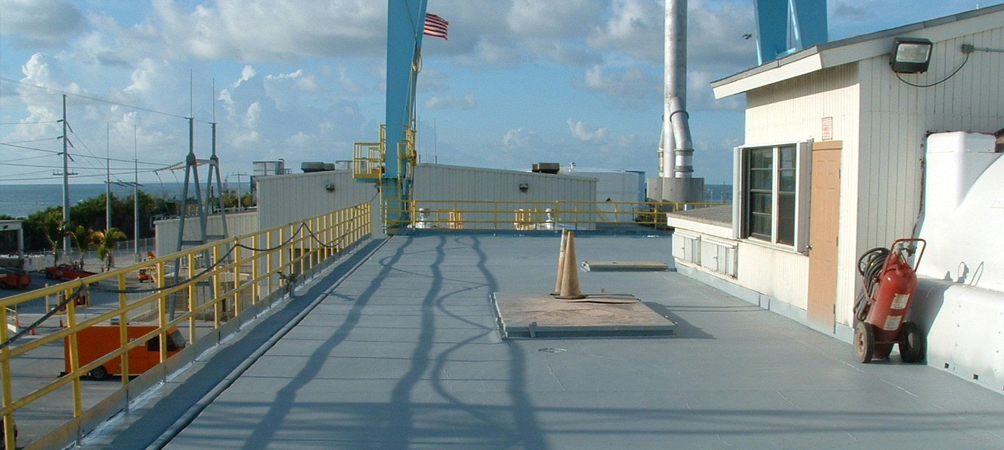
PROJECT DESCRIPTION
Key Utilities was experiencing leaks through pre stressed concrete roof. Water was leaking in various rooms below. Polyurea was chosen because of its proven history. Another factor was the UV stability. Fast set & cure time was of the essence as we were in the middle of rainy season. The concrete roof was water blasted to remove the existing paint. Cracks were repaired and a solvent free primer was applied. 80 mils of polyurea were applied with a slip resistant texture. The roof made it through the rainy season and is still leak proof today.
LEE COUNTY WATER UTILITIES (LCWU)
Location: Fort Myers, FL
System Applied: PW101 – Visuron Technologies, Inc.
Substrate / Area: Metal Tank Primary Containment
Date Completed: July 2002
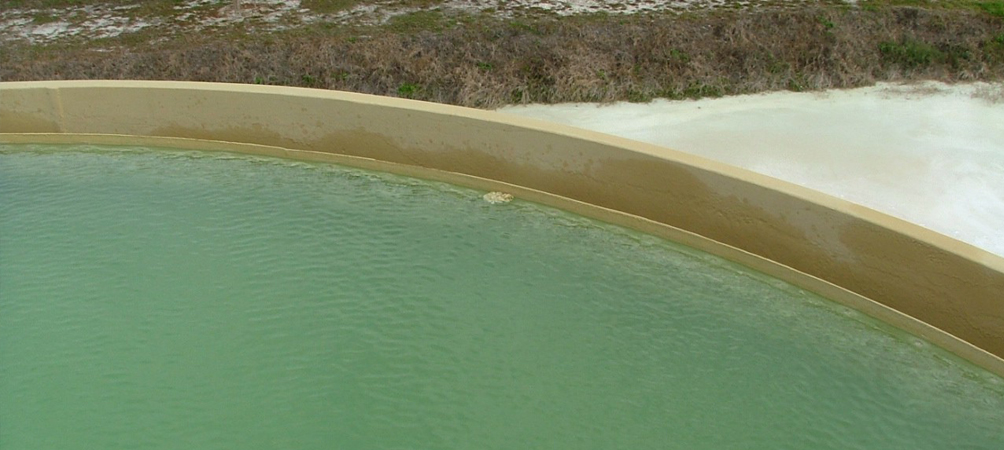
PROJECT DESCRIPTION
Lee County Water Utilities (LCWU) needed to re-coat launderer in their clarifier. The multiple layer of paint was failing after 1 year of resurfacing. Polyurea N.S.F. was chosen because of its rapid return to service and proven history in the water & waste water environment. The clarifier launderer was sandblasted to remove multiple layers of paint to white metal. A minimum of 80 mils was applied encapsulating the launderer and metal support preventing any further rust of clarifier. The polyurea shows no wear as the counter part would be schedule for another paint job.
PATRICK AIR FORCE BASE
Location: Cocoa Beach, FL
System Applied: JBT 303
Substrate / Area: Concrete, Secondary Containment / 28,000 sq. ft.
Date Completed: October 2006
Quality Control: Primeaux Associates, LLC.
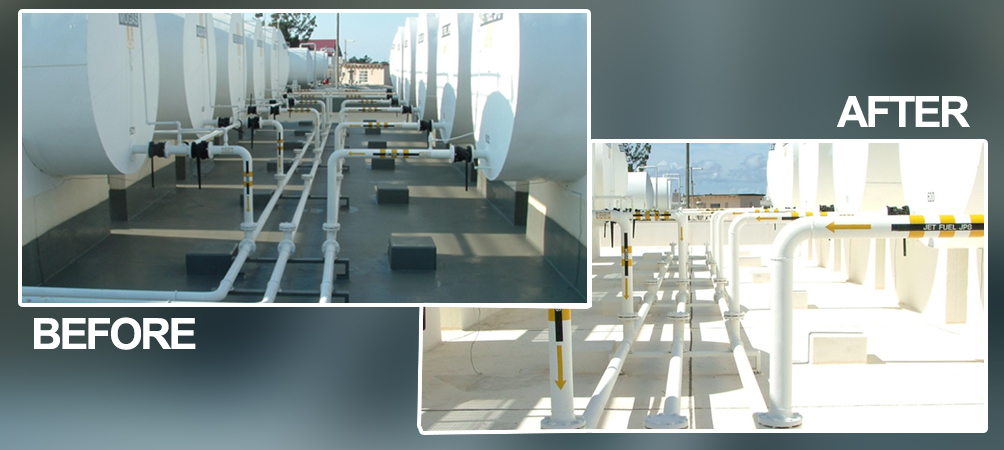
PROJECT DESCRIPTION
The main diesel and aviation fuel storage secondary containment area was not performing as had been designed. Several cracks had appeared over the years along with the deterioration of the expansion joint; material was failing.
As timing, due to weather conditions, was very important, the seamless polyurea spray system was chosen. This system has a rapid cure time along with excellent chemical resistance to the contained fuels. The concrete area was in poor condition. Previously applied paint was peeling and the attempted repairs to the expansion joints were failing.
The concrete was pressure washed using a hot aqueous solution of Bio-Solve to remove contaminants and peeling paint, then rinsed. This brought the concrete to a good condition with good texture and cleanliness, therefore blasting was not required. The complete area was primed with a emulsifiable polyurethane primer for adhesion enhancement and reduction/elimination of concrete out gassing. The polyurea system was applied at a nominal thickness of 80-100 mil with a slip resistant texture.
There were several days where rain called for application interruptions. The rapid cure of the polyurea system was unaffected by the rains. The polyurea system was applied up the wall and onto the 36 tank supports to create a seamless bonded containment membrane. Application was completed in 7 days.
PCB CONTAINMENT ICA OF JACKSONVILLE
Location: Jacksonville, FL
System Applied: JBT 303
Substrate / Area: PCB Containment / 38,000 sq. ft.
Date Completed: November 2005
Quality Control: Primeaux Associates, LLC
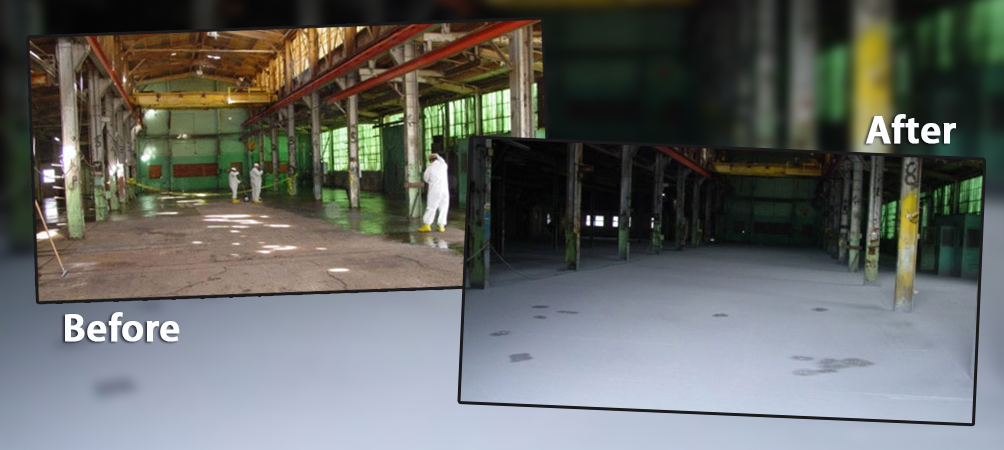
PROJECT DESCRIPTION
The building was scheduled for demolition, but the existing slab was impacted with PCB. It was necessary to protect the slab. Many different products were considered from multiple lifts of asphalt, concrete, plywood, HDPE. Polyurea was the product of choice being a seamless, low perm material that would also stand up to the equipment used to demo the structure. Another factor was the price of disposal of the slab and cap after demolition would be greatly reduced. Approximately 8 tons of polyurea was used versus 100 tons of other materials.
Polyurea was selected. The concrete was water blasted with a hydro carbon solution and primed with P3 primer. Polyurea was then applied, 60 mils in low impact area and 120 mils in heavy loading and impact area.
After demolition of building was completed, the cap was inspected. The only damage to cap was from dropping beams. All areas where beam punctured surface were easily repaired. The overall performance of cap was better than expected.
ACID CONTAINMENT UTILITIES, INC.
Location: N/A
System Applied: Polyurea PolyVers LC25, PolyVers VT40
Substrate / Area: Acid Containment
Date Completed: January 2007
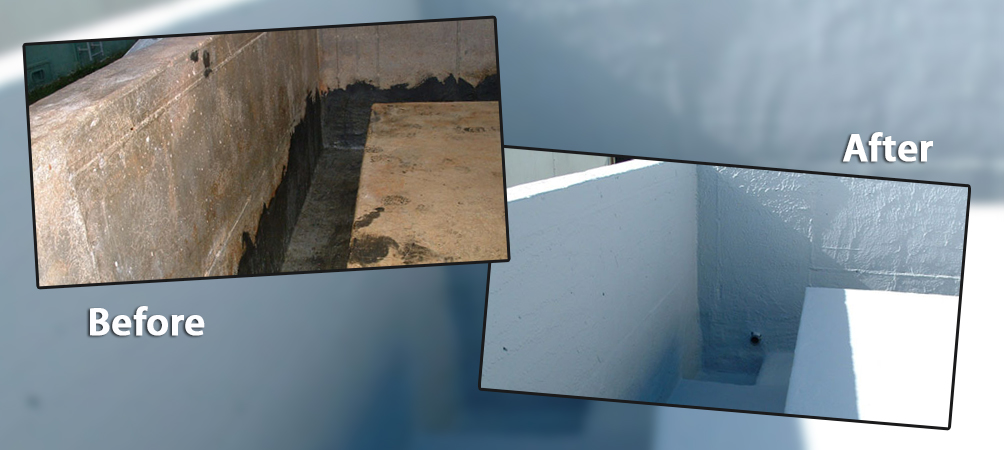
PROJECT DESCRIPTION
The acid containment’s existing system was failing. The system was removed and hydro blasted to remove bonding agent. Surface then was neutralized to accept primer. Surface had to be skim coated where acid had deteriorated the containment. P3 primer was applied followed by 60-70 mils of polyurea. A primer coat of PolyVers LC25 Extreme Chemical Exposure Lock Coat was then applied and top coated with PolyVers VT40 Finish Coat. RoboLiner ®was used to replace the old system.